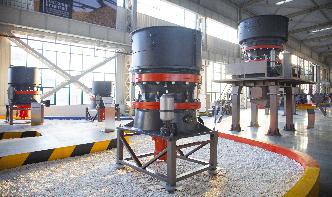
iron ore sinter concentrate pellet fines
Main feed into a sinter plant is base mix, which consists of iron ore fines, coke fines and flux (limestone) fines. In addition to base mix, coke fines, flux fines, sinter fines, iron dust (collected from plant dedusting system ESP) and plant waste are mixed in proportion (by weight) in a rotary drum, often called mixing and nodulizing drum.