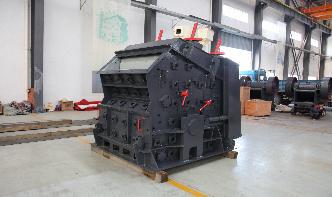
Oversize Reduction Project at the Iron Ore Company of ...
Description. The Iron Ore Company (IOC) of Canada Mining and Operations Departments expressed an interest in reducing the amount of oversize material (>1 m × 1 m × 1 m) being produced and its subsequent downstream effects including inpit sorting and reduction, damage to mobile equipment, and significant delays in the loading pockets and the primary crushers.