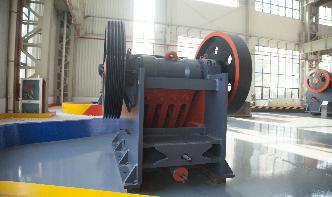
Optimization of mill performance by using
The performance of tumbling mills is sensitive to the volumetric mill filling which influences grinding media wear rates, throughput, power draw, and product grind size from the circuit. Each of these performance parameters peaks at different filling values.